Exploring the World of Metal Stamping: From Layout to Manufacturing
Within the world of manufacturing, metal stamping sticks out as a precise and efficient method for shaping metal sheets into different types with exceptional uniformity. From the first layout stage where detailed patterns form to the intricate production processes, metal stamping is a blend of artistry and engineering. Looking into this world reveals a complicated interplay of imagination and technological mastery, using a look into a realm where technology meets craftsmanship.
History of Steel Stamping
Metal stamping, a commonly made use of production procedure today, has a rich history that dates back to ancient times (Metal Stamping). The beginnings of metal stamping can be mapped to old civilizations such as the Egyptians, who used marking strategies to embellish jewelry and accessories with intricate styles. In time, metal stamping evolved, with people like the Greeks and Romans utilizing it for creating coins and decorative things
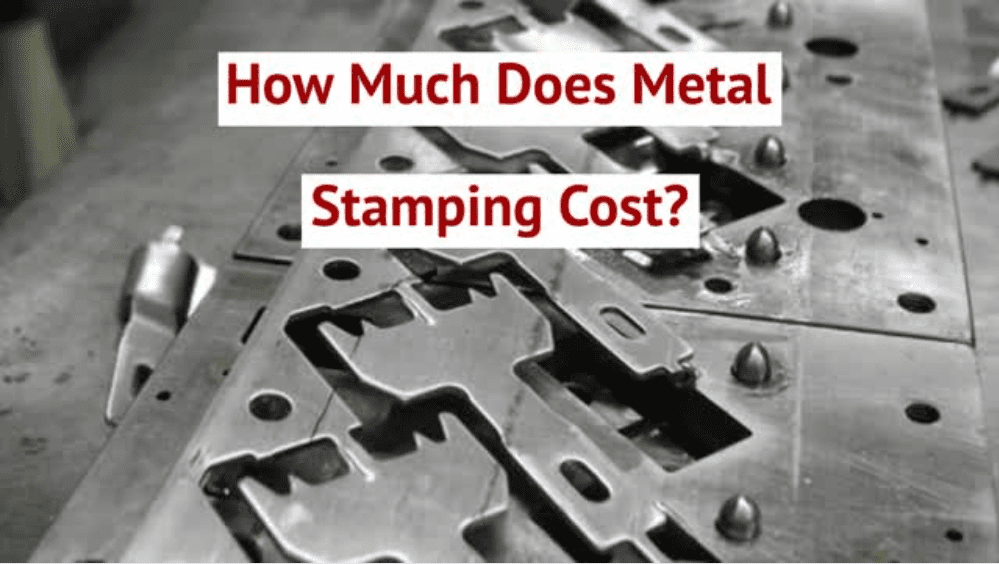
In the 20th century, steel marking continued to advance with the combination of automation and computer mathematical control (CNC) technology. These innovations even more increased the performance and precision of steel stamping procedures, making it a vital part of modern-day manufacturing throughout markets such as automotive, aerospace, and electronic devices. Today, metal stamping continues to be a crucial manufacturing procedure, combining practice with development to fulfill the demands of a constantly progressing industry.
Layout Considerations and Prototyping
When developing metal marking projects, careful attention to design considerations and prototyping is essential for making certain ideal production end results. Layout considerations in metal stamping consist of product selection, part geometry, tooling style, and manufacturing feasibility. Choosing the ideal product is crucial as it affects the component's efficiency, price, and manufacturability. Part geometry influences the complexity of the marking procedure and the capability of the end product. Tooling design plays a considerable duty in the success of steel stamping projects, affecting component precision, tool longevity, and production performance.
Prototyping is a vital phase in the steel stamping procedure that allows designers to evaluate the layout, verify manufacturability, and make required changes prior to full-scale manufacturing. By thoroughly considering style aspects and making use of prototyping, makers can streamline the steel stamping procedure and achieve high-grade, economical production end results.
Tooling and Devices Essentials
Taking into consideration the critical function that tooling layout plays in the success of metal stamping projects, recognizing the essential devices and tools called for is extremely important for achieving efficient you could try these out production outcomes. Fixtures hold the metal in area throughout the marking procedure, making certain precision and repeatability. Spending in high-grade tooling and equipment not just improves manufacturing performance yet likewise leads to higher accuracy, decreased waste, and general cost savings in metal marking procedures.
Production Process and Quality Assurance
Successfully managing the manufacturing procedure and executing robust top quality control procedures are vital for guaranteeing the success of metal marking projects. The manufacturing process in metal marking involves a collection of steps that must be meticulously worked with to achieve optimum results. It starts with the prep work of resources, adhered to by the configuration of the stamping devices and tooling. Operators then feed the products into the press, where the marking operation takes place. Throughout this procedure, it is important to monitor the assembly line for any type of problems that may affect the high quality of the stamped parts.
Quality assurance in steel stamping is vital to deliver products that satisfy the needed requirements. Inspecting the stamped parts at different phases of manufacturing aids identify any problems early, protecting against costly rework or scrap. Techniques such as dimensional assessment, visual assessment, and product testing are typically used to make certain the top quality of the stamped components. By keeping stringent quality assurance requirements, makers can support their track record for providing premium metal stamped items.
Applications and Sector Insights
In the realm of steel marking, the successful application of manufacturing procedures and quality control measures directly affects the performance and reliability of different sector applications and offers important insights right into the field's functional characteristics. Furthermore, metal marking helps with the production of different household devices, including fridges, cleaning machines, and read this post here stoves, by find out this here supplying affordable services for making sturdy and complex components. Comprehending the applications and sector understandings of metal marking is crucial for enhancing production procedures and improving item quality throughout various markets.

Final Thought
Layout factors to consider, prototyping, tooling, devices, production procedures, and high quality control are necessary facets of metal marking. With its prevalent applications and market insights, metal stamping proceeds to be a flexible and effective production procedure.